The thermic applications involving fans are present in several areas of the industry, and the OEMs integrating fans in their own machines are going from the boilers manufacturer, burners, oven specialists, dust suppression suppliers..
Each of them has special need with different specifications, but all are requesting reliable material and high efficiency because the fans are operating 24/7during many years. The following functions are ensured by fans with particular characteristics according the challenge.
- Combustion: fans often high pressure for the fluidized bed furnace or for the pulverized fuel burner.
- Cooling: reliability and energetic efficiency: for example, to ensure the life length of the side-shield oven or the float tin bath in glass industry.
- Smoke extraction: the fan is considered as the lung of the installations including combustion. The speed regulation ensures a light depression in the oven or incinerator, whatever the production regime.
- Recycling and/or reheating: the design of the fan should be suitable for high service temperature (up to 800°C), and if any oxidation of the product should be forbidden, the fluid transported might be a mix of oxygen and hydrogen: the
fans must be rigorously gas tight and ensure a secured operation of the installation.
- Smoke dust suppression: the fan is generally installed downstream, close to the chimney. According the flow and the system pressure drop, the motor power range might be important (from 132 kW up to 2500 kW). Despite the
reliability, the operation might be noiseless, because the noise duct level is emitted by the smoke evacuation chimney
The fans in contact with hot fumes need a compatible design with the important operating temperatures, involving several particular precautions.
- Steel selection: the standard carbon steel is used up to 350°C average, but if the impeller is presenting important mechanical constrains, we prefer to select steel with 500 N/mm² or 700 N/mm². From +/- 650°C, the steel starts to melt and the choice of the alloy composition is becoming a key point to be calculated, going from the heat-resisting steel type 309 and 310 to the special alloy as for example 253 MA of Avesta or the HR120 from Haynes. When operating at temperature, the dew point gas is often exceeded, ensuring the harmlessness of corrosion. However, when operation circumstances showing any risk of condensation, the steel used will go from simple Inox 304 to the more elaborated alloy, according the gas aggressivity.
- The bearings supporting the shaft are particularly sensitive to the temperature and the integrity of the oil or grease lubrication should be ensured, despite the heat conduction through the shaft transmission. The calories dissipation system has to be set up between the casing and the first bearing house thanks to a cooling impeller in aluminum fixed on the shaft or discs with blowing cool air thanks to an auxiliary fan.
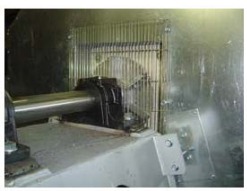
- On the larger fan size, the steel expansion is about 1mm per meter and per 100°C forcing to adopt the shaft line as reference fix point. The use of supporting columns of the casing at the shaft height allows the free expansion upwards and downwards, avoiding any contact of the impeller with the inlet bell mouth, or the contact of the shaft with the crossing hole through the casing. The flexible connections are useful to avoid contact with the pipes downstream and upstream. Indeed, the pipes dilatation might cause unwanted forces on the fan’s counter flanges…
- The people safety and energy cost saving are both a reason for insulating the fan casing thanks to Rockwool and a galvanized steel strip protection. If the fan is integrated into an acoustic cladding, it is necessary to prepare the calories dissipation through forced ventilation with inlet/outlet silencers, to avoid a motor excess heating.
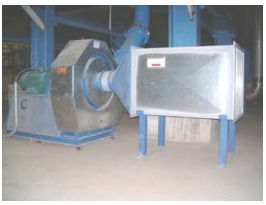
- We are often requested for the dampers, either “regulation” or “on-off” for the gas or fumes pipes. The same steel use precautions and protection of the guiding valves should be applied to that equipment. When it is question of flue dampers straight after the oven, the damper shell might be even protected with refractory concrete.
AirVision is strong of various fan references used in the thermic applications, for example :
- Fumes exhaust fan on glass furnace
- Recirculation fan HNx on continuous annealing furnace in iron and steel industry
- Fumes exhaust fan on domestic and industrial waste incineration plant
- Exhaust fan on waste heat boiler
- Recirculation fan in the wood dryers, bricks dryers, …
- Air combustion fan high pressure
- Cooling fan on sidewalls tin bath or glass furnace
- Etc.